Installation Tips for Assembling Hydraulic Hoses
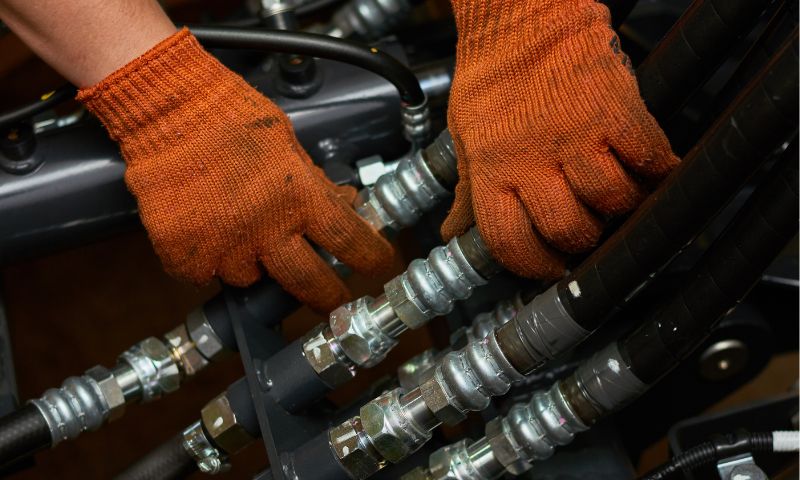
Are you installing a hydraulic hose system in your industrial workplace? While you do, keep our installation tips for assembling hydraulic hoses in mind to ensure that you install it right the first time and make future maintenance and repairs easier.
Avoid Twists and Kinks
The most significant problems to avoid when installing hydraulic hoses are twists and kinks. Anyone who has operated a garden hose knows what happens when there’s a kink or twist. And when that occurs with hydraulic hoses, it could cause significant pressure loss or even ruptures in the hose.
A hydraulic hose should always bend on one plane only. If it has even a slight twist, it’s more likely to degrade and lose pressure as it ages. It can be difficult sometimes to tell how twisted the hose is when connecting, so double-check the labeling and wiring on the hose or make a mark on the hose yourself to ensure it’s not twisted when installing.
Stay Within the Hose Bend Radius
Another important installation tip for assembling hydraulic hoses is always to ensure the hose is within the bend radius. The hose bend radius is the distance to the inside edge of the hose when making a 90-degree bend.
If the hydraulic hose bends too sharply or exceeds its bend radius, it’ll be much more likely to distort beyond its capability and fail. Overbent hoses are likely to rupture or leak. At the very least, they may lose pressure. And remember that an ample straight section should precede every bend in a hose, typically twice as long as the hose diameter, to lessen the impact of the high-speed fluid on the bend.
Accommodate Hose Movement and the Surroundings
While it may seem that you’ve installed the hoses properly and the hose route is safe, don’t forget to consider the hose’s movement and surrounding surfaces. When the hydraulic system runs, there will be some movement from the hoses. As a result, it’s always best to err on the side of caution and give more space than needed.
If there are potentially abrasive surfaces near the hoses, especially if they move or vibrate while the system is in operation, they can cause leaks and ruptures as they touch the hose. If rerouting the hose away from the abrasive surfaces is impossible, you’ll have to consider clamping the hose.
Consider Future Access
When designing and installing the hydraulic hose assembly, you need to keep future access for maintenance in mind. Keeping up with hydraulic hose maintenance is critical to ensuring the longevity and functionality of your hydraulic hoses and reducing downtime when issues arise.
The hydraulic hose system may seem fine initially. But you should consider how easy it is to access components should a part or hose fail. Make maintenance and future repairs easier by considering long-term access to the system during installation.
Would you like to receive similar articles by email?

