Reasons Items Seem To Be Going Missing in Your Warehouse
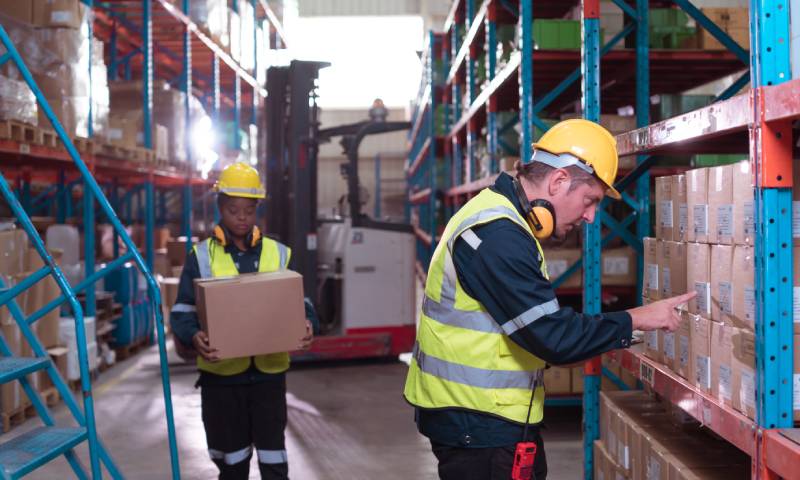
Do you often find yourself scratching your head, wondering why items seem to mysteriously vanish from your warehouse? If your inventory management system is showing incorrect stock levels and your employees are reporting discrepancies, rest assured you’re not alone. Missing items in the warehouse is a common issue that many businesses face, but the reasons behind it may surprise you. Here are some of the most common reasons items seem to be going missing in your warehouse.
Poor Inventory Management
One of the main reasons items go missing in warehouses is poor inventory management. Accurate inventory management is key to maintaining visibility over every item in your warehouse. Without it, items can easily become lost or misplaced, leading to confusion and inefficiency.
Take steps to prevent issues with inventory visibility. It could be that your items aren’t vanishing into thin air—they’re just difficult to locate due to ineffective tracking systems. Implementing a robust inventory management system can help you maintain accurate records and streamline processes.
Inadequate Warehouse Organization
A disorganized warehouse can easily lead to lost items. When storage systems aren’t well thought out, it becomes increasingly difficult to keep track of inventory. Misplaced items then become the norm rather than the exception.
Implementing a systematic approach to storage, such as using barcode systems or arranging items by frequency of use, can greatly improve organization and reduce the likelihood of missing items.
Employee Theft
As unfortunate as it may be, employee theft is another common reason for missing items in the warehouse. Employees might take advantage of lax security measures or lack of supervision to pocket items for personal use or resale.
To combat this issue, implement strict security protocols, such as limiting access to certain areas and monitoring employees through surveillance cameras. Additionally, conduct regular audits to ensure accountability and discourage dishonest behavior.
Inefficient Technology Use
Technology can be a great aid in warehouse management, but it can also contribute to missing items if it’s not utilized correctly. For example, if you don’t properly scan barcodes or update inventory in real time, stock levels may appear incorrect and lead to confusion.
Investing in reliable technology and providing proper training on its use for employees can help prevent this issue. You should also prioritize regular maintenance and updates to systems to avoid any technical glitches that could lead to missing items.
Inadequate Training
When team members aren’t adequately trained, mistakes are more likely to happen, leading to misplaced or lost items. Proper training ensures that everyone knows how to handle inventory correctly and follow established protocols.
Investing in regular training sessions can keep your team up to date on best practices. By ensuring everyone is well-versed in the latest techniques and technologies, you’ll minimize the chances of items going missing in your warehouse.
Addressing the reasons items seem to be going missing in your warehouse is the first step in preventing it from happening in the future. By properly organizing and managing inventory, you can improve your order fulfillment process and experience a more successful business.
Would you like to receive similar articles by email?

