4 Essential Saws for Metal Fabrication Shops
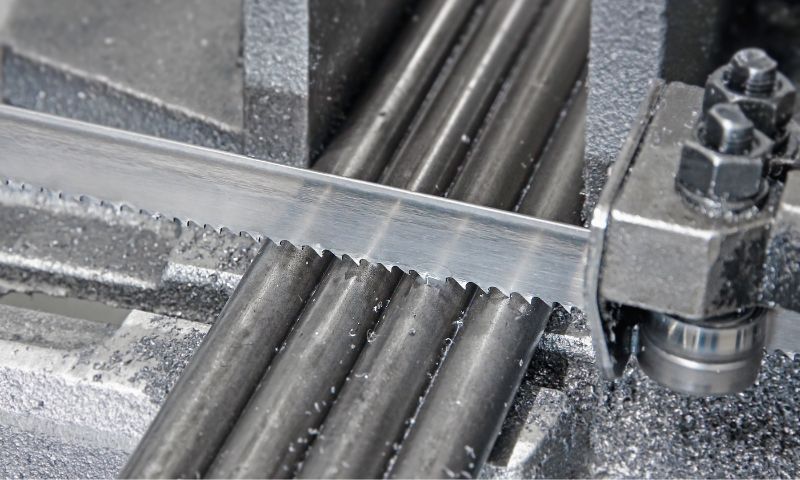
In the complex world of metal fabrication, precision and efficiency are not optional; they are the pillars that support the entire industry. Thus, saws are essential tools of the trade. The right saw can be the difference between smooth, streamlined operations and a project mired in inefficiencies. Let us explore four essential saws for metal fabrication shops.
Band Saws
With its continuous band of toothed metal rotating on two wheels, the band saw is renowned for its precision and flexibility. It can handle intricate cuts, curves, and also bevels, making it ideal for a range of metal types. The band saw blade’s teeth can vary to suit different materials, ensuring a steady and even cut. Newer models even integrate features like automatic feed control and CNC compatibility, allowing for unerring precision. Its versatility means the band saw is commonplace in almost every metal fabrication shop because it is trusted for both large-scale structural work and fine detailing alike.
Cold Saws
Unlike their abrasive counterparts, cold saws utilize toothed blades made of high-speed steel or tungsten carbide. This choice of blade, combined with their lower RPM, means cold saws produce minimal heat. Therefore, there is less distortion in the material and the finished edge often requires no further processing. Their ability to achieve tight tolerances makes these saws crucial in applications like pipe cutting, tube profiling, and structural steel, where accuracy is non-negotiable. With semi-automatic and electrically controlled models, cold saws are also at the forefront of the automation movement in metalworking.
Abrasive Saws
When raw power meets rugged efficiency, the result is the abrasive saw. With a large, abrasive-filled blade, these saws offer unmatched cutting speeds, making short work of even the toughest materials. Abrasive saws, sometimes called cutoff saws, are the tool of choice for quick and rough cuts on materials such as steel, aluminum, and stainless steel. They may not deliver the precision of their cold or band saw counterparts, but when speed and cost are paramount, abrasive saws shine brightest.
Chop Saws
Popular in smaller, more specialized fabrication operations, the chop saw combines elements of the band saw’s maneuverability with the abrasive saw’s power. A motorized saw with a fixed blade, the chop saw is excellent for straight cuts in smaller pieces of metal, often for custom fabrication or when cutting metals in construction projects. Chop saws have a limited cutting capacity compared to other saw types, but they are invaluable when it comes to personalization and prototyping.
Conclusion
By understanding the essential saws for metal fabrication shops, fabricators can improve their workflow efficiencies, reduce material waste, and produce high-quality work that stands the test of time. With modern advancements continuing to influence the landscape of metalworking, understanding the different types of saws and their applications is a step toward staying sharp in the industry. In the end, the right saw is not just a tool—it is a strategic investment in the productivity and quality of your metal fabrication shop.
Would you like to receive similar articles by email?

